Manganese Dioxide Dosing System
Inquip was commissioned by one of Australia’s largest clay brick manufacturers to change the delivery method of Manganese Dioxide from liquid to powder.
Inquip would achieve this by providing a fully automatic system to accurately discharge the powder from the bulkbag to the conveyor belt before mixing.
For the system to deliver the desired results, the accuracy of <1% was required, with the system to be made within an existing plant, leaving little margin for error in design.
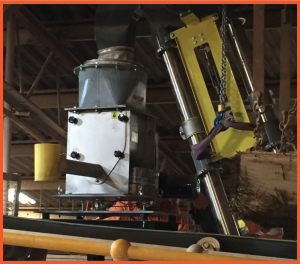
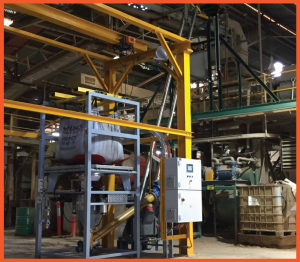
Solution
Inquip’s task was to provide a system of emptying bulk bags of Manganese Dioxide at a consistent percentage rate to the central conveyor belt. The system would need to have the capability to continually adjust the rate of dosing to match the amount of Manganese Dioxide v the weight of clay on the belt – therefore providing the perfect percentage of the blend to ensure high quality, consistent continuity of colour.
Our engineers conducted a site visit to establish the best possible delivery method and location to minimise site impact. A 3D model was then developed to ensure the project met all the requirements.
The electrical engineers at our sister company, Automation & Control, developed the system’s operation controls to integrate with the system via HMI and connection to the site’s PLC, to ensure data accuracy at all times.
Equipment
- Bulk Bag Unloader
- Screw Conveyor
- Full Control System
Outcomes
Following the installation of the system, the client has enjoyed a reduction in expenses and wastage associated with receiving the Manganese Dioxide in liquid form. The powered product mixes better with the clay to deliver a more consistent and homogenous blend, resulting in a superior finished product with reduced breakage.